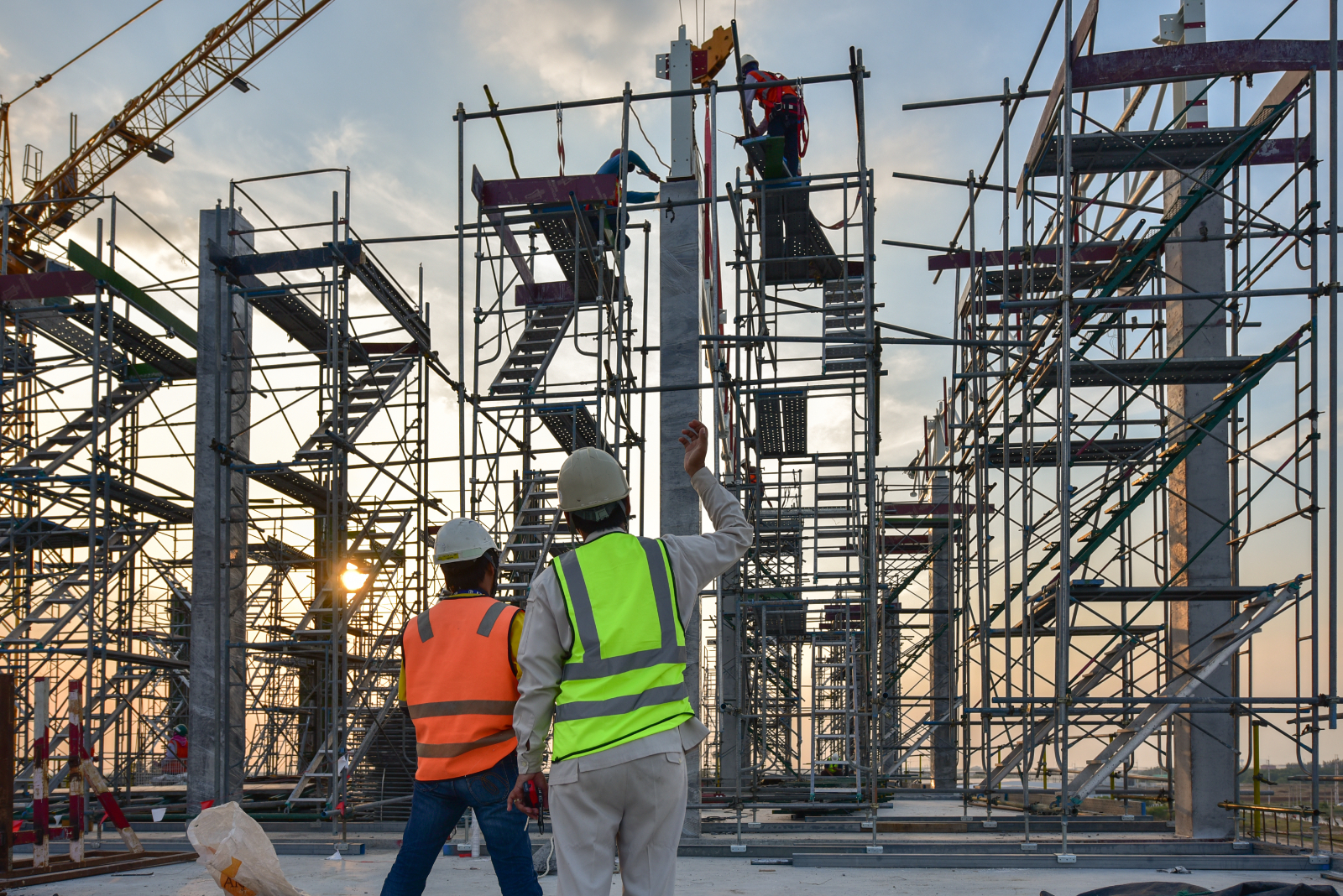
When project deadlines are looming, allowing periods of overtime can be helpful in ensuring everything is completed on time. However, excessive reliance on overtime during any phase of construction can be a tell-tale sign that something might have gone wrong at the initial planning stage.
So, the question is ‘How can a construction business effectively reduce its reliance on overtime and ensure smoother, more efficient operations?’ Read this week’s blog to explore this subject in more detail.
What’s the problem?
There are several reasons why excessive overtime is problematic for a construction company. As well as being costly, it can lead to worker burnout, decreased productivity and an increase in staff turnover. The use of overtime should therefore always be approached cautiously and action should be taken to reduce the need for it wherever that’s possible. Here are seven suggestions:
1. Plan ahead
The most successful construction projects begin with a detailed planning phase. Charting out the scope of the project in advance will give you a clear picture of the work that lies ahead. This will enable you to set up a well-defined budget and schedule, source the right amount (and type) of labour for each phase, and ensure that all project details are well communicated to your workforce.
2. Effective Communication
Talking of communication, even a brilliant plan will be ineffective if it isn’t effectively communicated to the people who need to follow it through. Investing in management staff that have the communication skills required to deliver clear and concise instructions will prevent confusion and disputes, ensuring everyone is on the same page.
3. Equip your workforce
Inadequate or outdated equipment can lead to decreased efficiency, ultimately meaning people will require more time to complete tasks (thereby increasing the chances of a project needing overtime). Ensuring workers have the best tools for the job will do the exact opposite. For example, think of how much time it might take to fasten a bunch of fixings using a manual screwdriver compared to a more efficient impact driver.
4. Streamline Meetings
Meetings are a necessary part of construction management, but they can quickly become a drain on everyone’s time. Minimise the number of meetings, keep them short and make them more efficient by getting straight to the point. This ensures that precious work hours aren’t wasted in prolonged discussions.
5. Prioritise training
Investing in training for your workforce can be a game-changer. Well-trained employees are not only more efficient but also less likely to engage in practices that cause delays and setbacks (again, reducing unnecessary overtime). Schedule training during downtime to ensure you’re not taking hands away from ongoing projects.
6. Go digital with admin
Embrace the power of modern automation technologies to increase productivity while minimising hours worked. Using advanced software for tasks like payroll management and other human resource systems can help reduce administrative burdens, leaving more time for your team to focus on their construction tasks.
7. Monitor and track time
To truly measure the impact of your efforts to reduce overtime, you must accurately track your workers’ time and there are lots of digital tools available that can help with this. The data you gather will help you to see how effective the measures you’ve implemented are and realise where adjustments might be needed.
Make overtime a rarity
When applied to a construction business, these strategies can not only reduce the reliance on overtime but also create a more efficient, productive, and worker-friendly environment. As a result, projects run like a well-oiled machine with overtime becoming a rarity rather than the rule.
30.10.2023
Feature image: Freepik