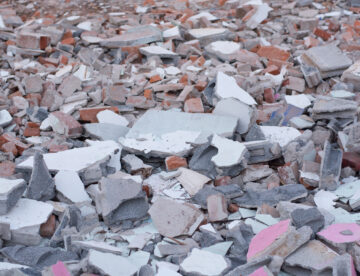
In a single year, the UK generates 67.8 million tonnes of non-hazardous Construction and Demolition waste, a figure that represents 62% of the nation’s total waste output.
This waste is made up of all kinds of products – concrete bricks, tiles, ceramics, insulation, wood, glass, plastic, bituminous mixtures, cement, gypsum, paints, varnishes, soil, stones, coal, tar, cables, pipes, adhesives and sealants – to name a few!
While much of this is recovered, taking action to reduce construction waste has proven to be good, not only for the environment, but also for business. Keep reading to find out more…
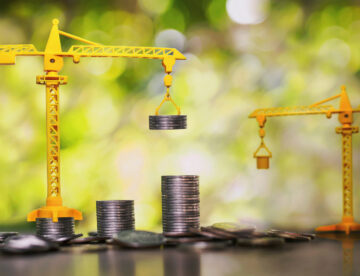
The cost of living crisis is something that’s repeatedly filling our news streams with reports of how this is affecting people, businesses and whole industries.
Now, it has been revealed that, during 2022, high levels of inflation on building materials has made its mark on the UK’s construction sector – taking the total cost of construction output for the year to a record level of £204bn.
Read on for more on this story as well as what the experts are predicting for 2023…
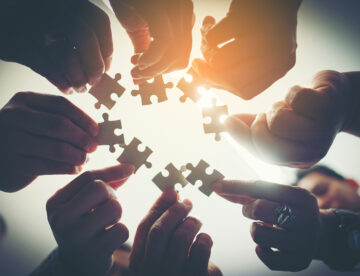
Having a well-functioning team is one of the most important factors which the success of any construction project relies on.
It’s how people from all kinds of backgrounds, with different skills and experience, find a way to work and cooperate with each other to reach a common goal; and how they maintain high levels of productivity, alongside excellent quality control and safety practices.
However, achieving and maintaining great teamwork does require some effort so, in today’s blog, we’ve got five tips for you.
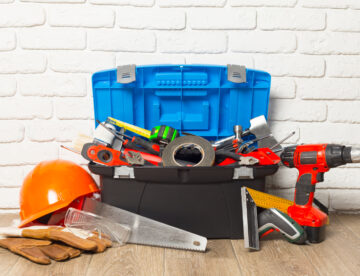
Tools and equipment are essential to the effective running of any construction site but, because they are used so much, they can suffer a lot of wear and tear, become damaged and eventually be unusable.
However, with proper care and maintenance, the lifespan of your tools and equipment can be extended and that’s good news for four reasons: 1) Better quality tools means better quality work; 2) It reduces costs related to repairs or replacements; 3) There will be fewer accidents/ injuries from faulty equipment; and 4) It’s better for the environment.
With so much to gain, in this week’s blog, we’re sharing some top tips for how to protect and maintain those tools.