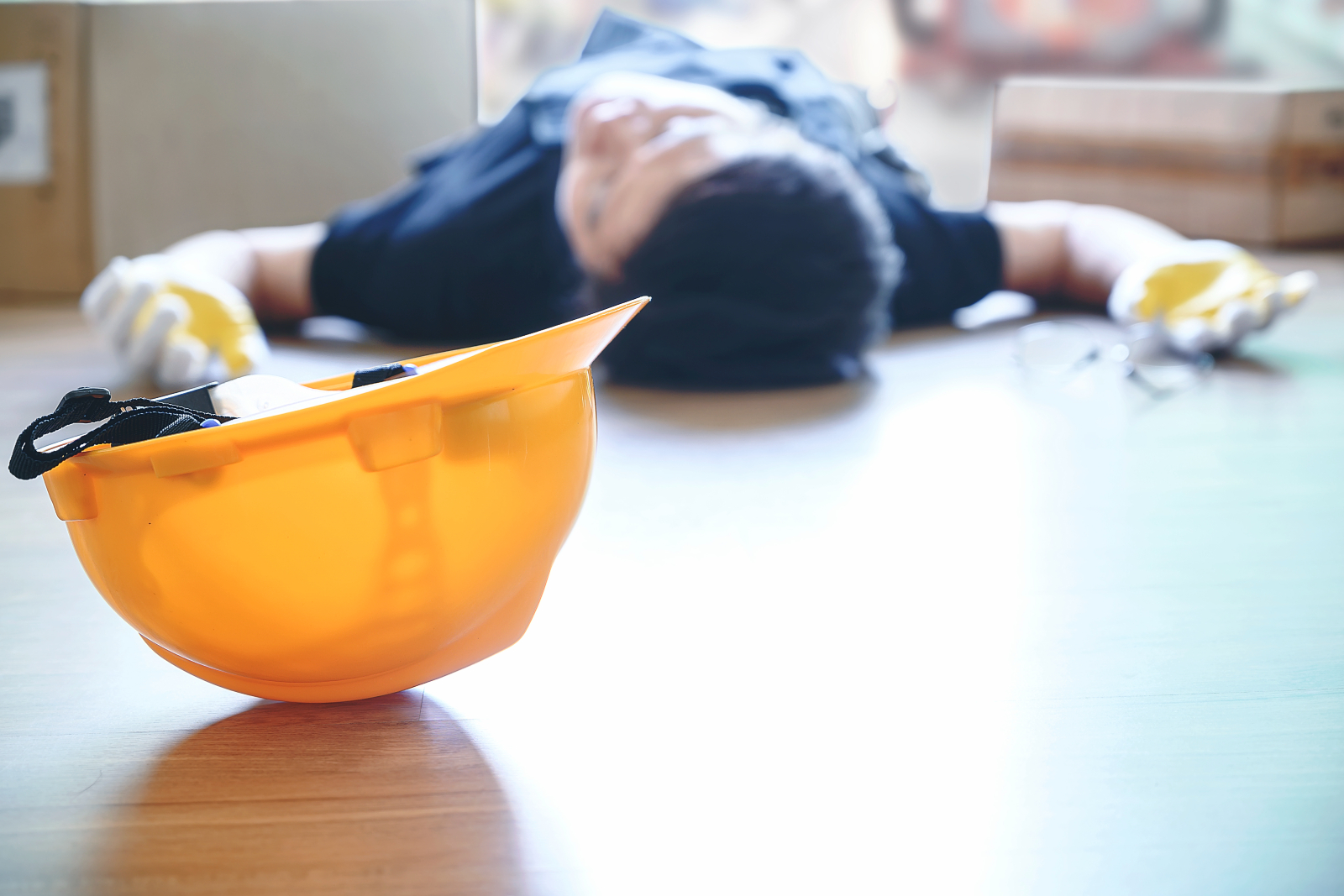
While strict health and safety measures have certainly reduced the number of injuries and fatalities in construction, the industry is still one of the most hazardous in the UK. Last year, construction workers suffered 61,000 non-fatal injuries and 40 people died as a result of workplace injury in our sector.
What’s most frustrating to anyone with an interest in health and safety is that the vast majority of on-site injuries are completely preventable. Today, we’re taking a look at four of the most common causes of accidents and offering some basic tips on what you can do to reduce the risks.
Working at Height
In 2020, falling from heights caused 19% of non-fatal injuries in construction and was also the top cause of deaths (47%).
Alongside the physical injury, such falls can leave people out of work for some time while they recover and be costly for employers too. Just recently, an investigation into an accident where a worker fell 5 metres, breaking several vertebrae in his lower back, resulted in the building contractor being fined £15000 and ordered to pay legal costs of £3,742.
Speaking after the hearing, HSE inspector Andy McGrory said: “The incident could have easily been prevented with simple precautions including properly planning the work, undertaking a suitable risk assessment and by selecting, erecting and using suitable work at height equipment for the job.”
The Working at Height Regulations 2005 requires employees to avoid the risk of falling by carrying out tasks on the ground if possible. Where working at height is essential, employers must ensure precautions are taken to reduce the chance of falls. This means:
- Conducting thorough risk assessments before any work commences
- Establish a safe method of working, including using suitable equipment, wearing the right gear and carrying out regular site inspections
- Ensuring workers have certified training in working at heights and providing adequate ongoing supervision.
Manual Handling
Statistics from the HSE for 2019/20 show that, alongside the 61,000 injuries mentioned above, the construction industry recorded 81,000 cases of work-related ill health. Most common were musculoskeletal disorder like sprains, carpal tunnel syndrome, back pains and bone fractures.
Poor manual handling was often the cause of these illnesses with workers overusing their muscles or placing too much strain on them. Here are some key DOs and DONTs:
DO:
- Always assess the health and safety risks of manual handling tasks
- Stick to what you’ve learnt in training about correct manual handling techniques
- Ensure the workplace environment is safe and report issues to a supervisor immediately
- Know your weight limits and ask for help if it’s needed
- Only use well maintained equipment and PPE where necessary
- Make use of relevant machinery where this will aid the task (e.g. a tail lift)
- Maintain good posture, fitness, health and flexibility
- Take on board any recommended changes to your regular practices
- Report any accidents/ injuries immediately and seek medical advice wherever necessary.
DON’T:
- Lift loads which you find too heavy
- Continue with jobs which require awkward body movements or repetitive movements if they haven’t been properly risk assessed (e.g. bending over for too long or squatting down)
- Use any unsafe manual handling techniques
- Use any PPE which is damaged or which would affect body movement or lifting
- Avoid mandatory training or ignore any important manual handling regulations
- Keep personal health issues secret if they could pose a risk to you at work.
Noise
The Control of Noise at Work Regulations 2005 requires all employers to minimise workplace noise levels. While that might be relatively simple for some sectors, in construction where’s there’s always noise from working activities and machinery, it’s not so straight-forward.
The problem comes when noise is excessive and/or constant as this kind of working environment can lead to workers suffering from long-term ear damage including permanent impairment. Some tips to address this include:
- Select tools with low sound emissions
- Set up barriers/ screens to reduce the noise to a safer level
- Use proper PPE during noisy tasks (e.g. earplug or muffs)
- Follow the guidance/ training on how to operate all plant machinery correctly as this can also help to reduce noise (e.g. the correct use gears on heavy machinery).
Electrical Cables
Around 1000 employees experience electrical accidents every year. Causes vary, including using an unsafe method of work; contact with exposed electrical cables; incorrect wiring; allowing unqualified workers to manage electrical tasks; uninsulated power lines; and poor maintenance of equipment.
Adherence to the Electricity at Work Regulations can minimise the risks of electrical accidents. To follow the rules, companies should be:
- Establishing safe working systems
- Routinely checking all tools, equipment, and facilities for defects. For electrical equipment, this can be done via a Portable Appliance Test (PAT).
- Training the workforce to ensure everyone is aware of the hazards that come with electrical work and know how to avoid/reduce risk.
Prevention is better than the cure
It’s unlikely that a construction site will ever be entirely hazard free but, as we said at the beginning of this article, most accidents and injuries are preventable. To make sure your site focuses on prevention and doesn’t have to deal with the cure, remember these five key points:
- Adhere to HSE regulations
- Carry out risk assessments
- Establish safe methods of working and stick to them
- Maintain a dairy of regular checks/inspections
- Ensure workers are properly trained and qualified for the task given and have adequate supervision.
07.09.2021
Feature image: Freepik