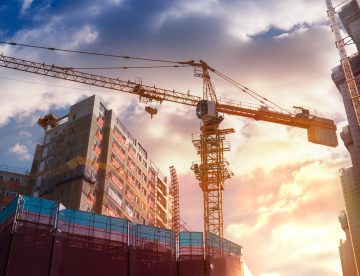
This week, the Egyptian city of Sharm el-Sheikh saw world leaders, business leaders, climate activists, civil society representatives and others arrive for COP27 – the largest annual gathering on climate action. Running for two weeks (until 18th November), this United Nations conference is seeking renewed solidarity between countries to urgently tackle the global climate emergency and deliver on the Paris Agreement for people and the planet.
Approaches that can be made by energy intensive sectors such as oil, gas, steel and cement will be discussed on the conference’s ‘Decarbonisation Day’ (11th November) so we’ll be keeping a watch on what’s said. Meanwhile, we thought we’d take this as our theme for this week’s blog and look at five ways construction companies can lower their carbon footprint.
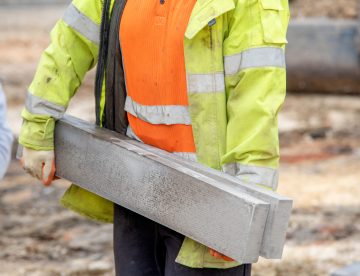
Lifting and moving heavy objects are part of normal working life on construction sites but, when managed badly, these everyday tasks can lead to damaging musculoskeletal disorders that leave workers struggling to stand, walk or sit down. For some, the injuries result in them having no option but to stop working in the industry altogether.
Because the health of workers can be affected to such a serious degree, inspectors from the Health and Safety Executive will be carrying out 1000 site inspections in October and November, particularly checking how workers are moving heavy or bulky materials. Read on for more details.
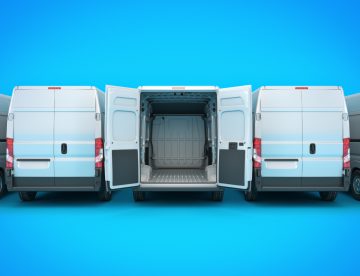
For most tradespeople, their van is not only a means of getting to and from work but also a vital part of their livelihood, holding many of the tools and materials they need to fulfil the day’s work.
How you fit out and organise your van can make a big difference in terms of the lifespan of your tools and equipment and also how efficient you are able to be on the job. With theft from vans being quite common, security is another major concern.
This week, we’re sharing five tips which could help you make sure your van is practical for your needs, well-organised and secure – in other words, fit for work.
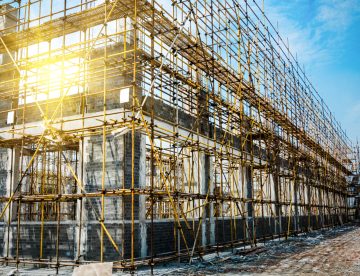
Whether it’s a small-scale conversion project or a large commercial development, the contractors and sub-contractors involved will have an impact on the community they’re entering into.
In all likelihood, the work will be carried out in a location where some people live, work or spend their leisure time and that means there are several areas of concern which should be taking into consideration – particularly the appearance of the site, noise control and the logistical arrangements.
How members of the public react to these impacts will largely depend on how well a contractor engages with them. So, in this week’s blog, we’re exploring why keeping good relationships with local communities is so important to the success of any building project and what can be done to maintain a reputation as a considerate contractor.
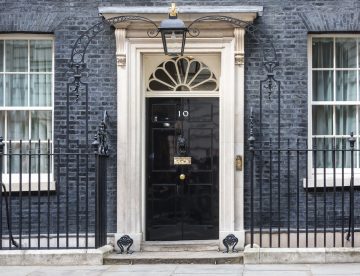
On 6th September, Liz Truss formerly became the UK’s 80th Prime Minister, moving into number 10 Downing Street and no doubt inheriting an in-tray as high as some of London’s skyscrapers!
In her debut speech as PM, Truss talked about her vision for an “aspiration nation” characterised by tax cuts and business-led growth, and talked about three priorities – tackling the energy crisis, supporting the NHS and boosting the economy. Claiming her mission was to “get the UK working, building and growing’, the new Prime Minister gave little detail of how that might come about and interestingly made no references to net zero, nature or climate change.
With the construction industry facing economic challenges around rising costs plus labour and materials shortages alongside environmental challenges around emissions, energy efficiency and waste, industry leaders have been quick to react to the new PM’s appointment. In this week’s blog, we’re sharing what some had to say.
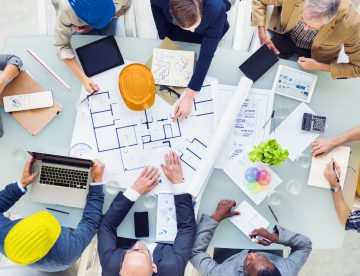
Over the past few weeks, we’ve been sharing what we know about some of the careers people can choose in construction. So far, we’ve looked at what it means to take up physical, on-site jobs like bricklaying and roofing but, while these are common and important roles, the sector offers a much broader range of possibilities than this.
In fact, construction is one of the biggest industries in the world and so there are literally hundreds of career pathways to choose from. For instance, there are Architects, CAD technicians, Quantity Surveyors, Site Engineers, Contracts Managers, Estimators, Construction Managers, BIM Coordinators, Commercial Managers, Health and Safety professionals, Environmental Consultants and a whole host of other back-office roles like accountancy, office management and digital marketing.
In this third and final part of our Careers in Construction series, we’re going to give a brief overview of five of these roles.
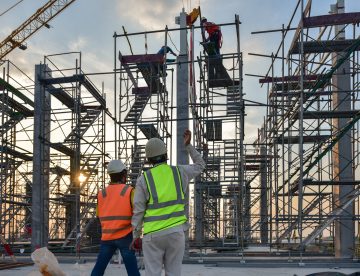
Over a quarter of a million extra construction workers may be needed by 2026, according to the latest Construction Skills Network report. That’s over 53,000 new recruits per year for the next five years!
Published annually by the Construction Industry Training Board (CITB), the report looks into the UK’s construction economy and makes key predictions about what will happen in terms of labour/ skills needs over the coming years.
Check out this week’s blog for more details of what this year’s report had to say plus what it means for the sector and our region.
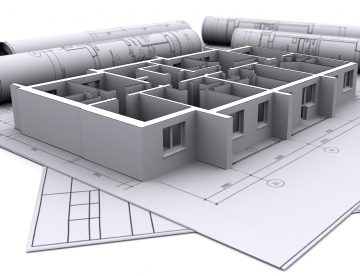
After a couple of challenging years, many had big hopes that 2022 was going to offer the construction sector a slightly easier path. However, as we now know, the challenges have continued to rain upon our industry – not least of which have been issues around the availability and cost of materials plus labour supply.
More positively, the sector seems to have retained its ability to adapt and love of innovation and these are qualities that can be clearly seen in some of the current architectural design trends. From incorporating more natural lighting to introducing more efficient processes into projects, the design work that’s happening right now is surely leaving its mark on the homes of the future. Keep reading this week’s blog for some of the top trends we’ve come across…