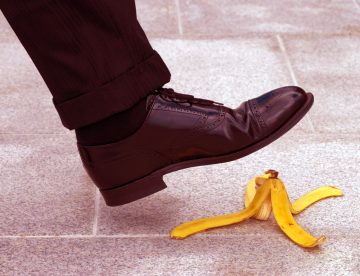
A few weeks ago, we published a blog with some tips about managing and improving something that plays a huge part in every construction project – quality. We looked at how important it is to set out goals, carry out tons of forward planning, create work lists for each and every phase of a project, make inspection plans and to monitor, review and learn from every experience.
However, even with the very best intentions to keep on top of all of this, once a project is underway those intentions can be slipped up and brought to the ground by unexpected obstacles or even by a single mistake that compromises quality and/or safety. As a follow up to our previous blog, today we’re delving into four key factors than can cause such a fall – Systems and audits, Changes, Materials and suppliers, and Human error.
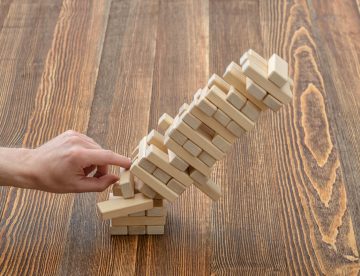
Mistakes can be made at any phase of a construction project. Some may be minor but others can have serious consequences, affecting costs, schedules and, of course, the health and safety of workers. When the stakes are this high, it’s important that any mistakes lead to lessons being learnt, but it’s even more important that they are avoided in the first place. With that in mind, here’s our short guide to avoiding some of the common pitfalls in construction; in other words what NOT to do!