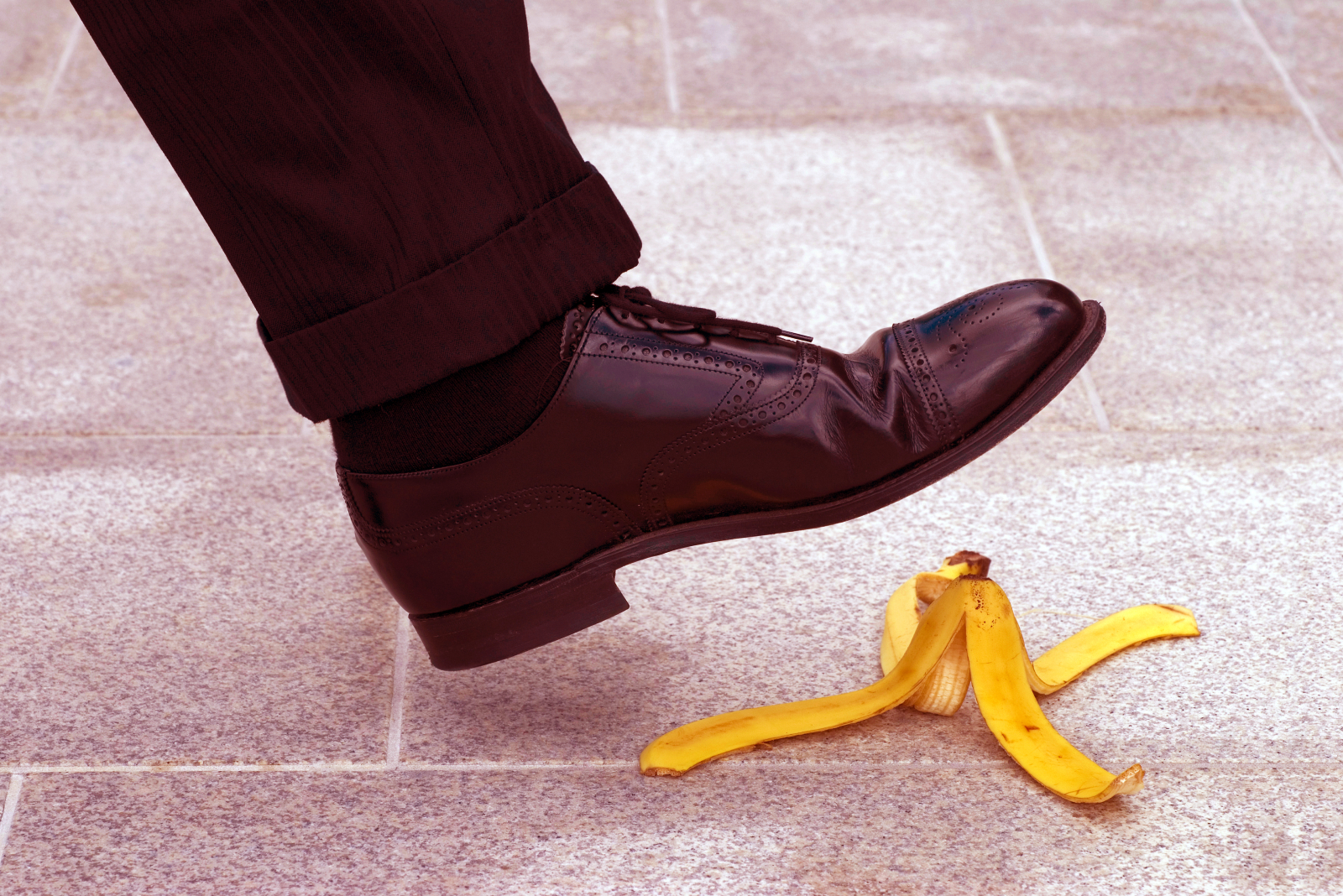
A few weeks ago, we published a blog with some tips about managing and improving something that plays a huge part in every construction project – quality. We looked at how important it is to set out goals, carry out tons of forward planning, create work lists for each and every phase of a project, make inspection plans and to monitor, review and learn from every experience.
However, even with the very best intentions to keep on top of all of this, once a project is underway those intentions can be slipped up and brought to the ground by unexpected obstacles or even by a single mistake that compromises quality and/or safety. As a follow up to our previous blog, today we’re looking into four key factors than can cause such a fall – Systems and audits, Changes, Materials and suppliers, and Human error.
1. Systems and audits
Not having a project management system in place: Having a well-defined management system for quality is the clearest way of ensuring that all works will undergo essential quality checks at times when it is most useful. Without this, there is a risk that the checks will be caried out too late, leading to errors/omissions and costly re-working. With many project management mobile apps now available, preparing a system that works for your project should be a fast and simple process.
Ignoring audits/testing: Sticking to a testing/auditing plan is only going to be useful if the reports are actually read and quality issues are acted upon. Sometimes this will go wrong because it isn’t clear who is responsible for reading the reports or making recommendations so the reports get bounced around from person to person while the quality issue just continues. Avoid this by clearly determining whose role it is to read and act upon audits/ test reports.
2. Changes
Undocumented changes or practices: Imagine a situation where one material gets substituted for another but the project documents don’t get updated. The mistake here isn’t the change of materials but the failure to record that change. The new material could have completely different needs around maintenance/ replacement but without any knowledge of this, future maintenance could be mishandled, thereby causing quality and safety problems. The use of digital has simplified the way documents can be kept up to date so always record those changes.
Last-Minute Changes: While small changes can be accommodated at last-minute, introducing late changes to any of the project’s essential features can lead to serious quality and sometimes dangerous safety issues. Set a deadline after which the key elements of design and engineering cannot be altered or, if a last-minute change becomes essential, make it ‘non-last-minute’ by extending the deadline, allowing enough time to test the changes before the final handover.
Scope Creep: Although many construction projects will change over time (e.g. as new information becomes available about site limitations), high levels of unplanned expansion in a project, known as ‘scope creep’, can be a serious quality concern. Without pre-planning, the increased scope might be tackled within inadequate budgets and timeframes, leading to corners being cut and an inconsistent levels of quality over the project as a whole. If scope creep looks likely to affect your project, go back to your management system and re-write the plans to accommodate the extra work.
3. Materials and suppliers
Poor-quality materials: Materials that are damaged or of poor-quality can cause all kinds of quality and safety issue in construction, failing to do what they’re supposed to do and reacting in unexpected ways during and after the building process. Think about what might happen if the concrete mix is wrong; if steel supplies have been incorrectly graded; or if what’s supposed to be weight-bearing timber isn’t strong enough to pass the test of time. Use suppliers you can trust and appoint a quality control officer whose job it is to verify all materials coming on site.
Supply failures: Aside from the problem of poor/ damaged materials, other supply issues that can affect quality include raised costs (this might result in some projects having to use lower quality materials to stay in budget) or short supplies (which might lead to a replacement brand being used, perhaps resulting in an unhappy client and time-consuming rework).
Make sure your key suppliers are aware of your expectations for the project from the outset and carry out spot checks to see if those expectations are being adhered to. While finding new suppliers in the middle of a project is not ideal, if there’s a persistent problem, this might be the only way to improve quality.
4. Human error
Workmanship: In many cases, defects or other quality issues will be the result of human error but why does this happen? Well, usually because of things that are totally avoidable, for instance hiring a subcontractor without verifying they’re fully qualified for the job or failing to provide the necessary training so that workers have the skills they need to perform to the required standard. Screen your subcontractors carefully and ensure training is provided and taken up by all who need it for their work.
Miscommunication: Last, but certainly not least, in this list are communication issues (or rather miscommunication issues) which almost inevitably lead to quality concerns. If instructions or advice is miscommunicated, that can lead to problems such as new techniques not being applied properly, design and engineering mistakes, or testing and inspection procedures going off schedule. Find a communications tool that works well for your team and keep everyone on the same page.
Overcome the obstacles and avoid that banana peel!
Just as it’s possible to avoid a nasty fall by stepping over or around a banana peel that’s been left on the ground, it’s equally possible to overcome the obstacles that can get in the way of quality in construction and save your project from the pain of a fall.
Simply being more aware of what could crop up is a good step in the right direction and following some of the tips we’ve included here and in our previous blog (published 17th May 2022) could really help ensure quality is well-managed and never becomes a major cause for concern.
If you’ve got tips or ideas that you believe would overcome any of the factors listed here or improve quality in general, let us know. Comment over on our Facebook or LinkedIn pages.
Related blog: Essential tips for managing and improving quality
06.06.2022
Feature image: Freepik (edited)