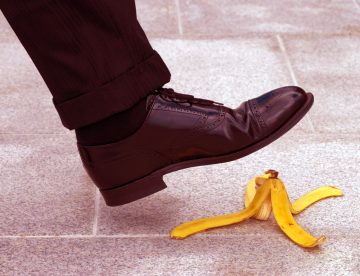
A few weeks ago, we published a blog with some tips about managing and improving something that plays a huge part in every construction project – quality. We looked at how important it is to set out goals, carry out tons of forward planning, create work lists for each and every phase of a project, make inspection plans and to monitor, review and learn from every experience.
However, even with the very best intentions to keep on top of all of this, once a project is underway those intentions can be slipped up and brought to the ground by unexpected obstacles or even by a single mistake that compromises quality and/or safety. As a follow up to our previous blog, today we’re delving into four key factors than can cause such a fall – Systems and audits, Changes, Materials and suppliers, and Human error.
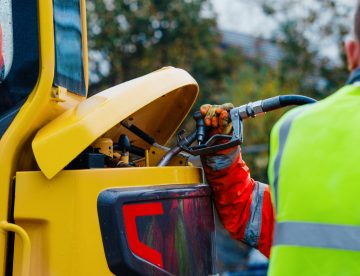
In new rules which came into place on Friday 1st April, the government has stated that construction firms in the UK can no longer use red (rebated) diesel for site plant and machinery.
Brought in as part of the search for policies which will help the country hit its net zero target by 2050, this would seem like a good thing. However, looking at the impact this is likely to have on construction companies in the current economic circumstances, many in the industry are calling this ‘the right policy at the wrong time’. Here’s what you need to know…
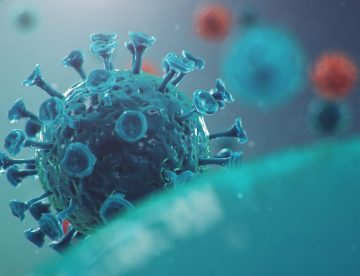
With so much uncertainty across the construction sector and in all our daily lives, today we’d like to present an update on where things stand at Sheriff Construction in relation to the impact from COVID-19. The majority of on-site work has come to a close Prior to the coronavirus crisis, Sheriff had contracts in place…