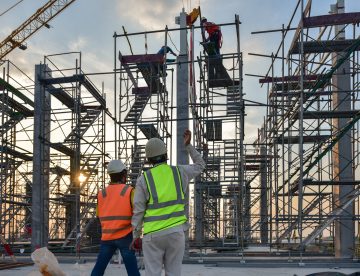
When project deadlines are looming, allowing periods of overtime can be helpful in ensuring everything is completed on time. However, excessive reliance on overtime during any phase of construction can be a telltale sign that something might have gone wrong at the initial planning stage.
So, the question is ‘How can a construction business effectively reduce its reliance on overtime and ensure smoother, more efficient operations?’ Read this week’ blog to explore this subject in more detail.
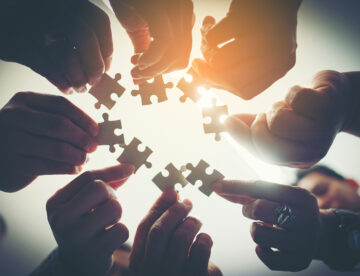
Having a well-functioning team is one of the most important factors which the success of any construction project relies on.
It’s how people from all kinds of backgrounds, with different skills and experience, find a way to work and cooperate with each other to reach a common goal; and how they maintain high levels of productivity, alongside excellent quality control and safety practices.
However, achieving and maintaining great teamwork does require some effort so, in today’s blog, we’ve got five tips for you.
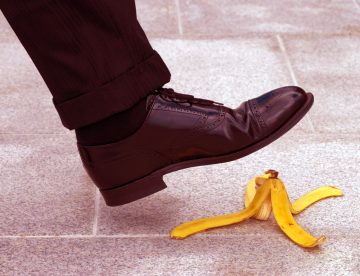
A few weeks ago, we published a blog with some tips about managing and improving something that plays a huge part in every construction project – quality. We looked at how important it is to set out goals, carry out tons of forward planning, create work lists for each and every phase of a project, make inspection plans and to monitor, review and learn from every experience.
However, even with the very best intentions to keep on top of all of this, once a project is underway those intentions can be slipped up and brought to the ground by unexpected obstacles or even by a single mistake that compromises quality and/or safety. As a follow up to our previous blog, today we’re delving into four key factors than can cause such a fall – Systems and audits, Changes, Materials and suppliers, and Human error.
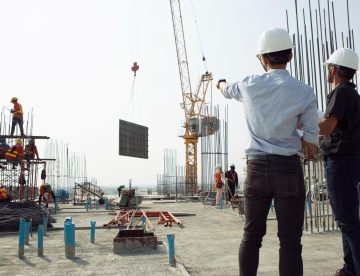
For any construction project, the position of Site Manager (sometimes referred to as Project Manager) is one of the most important. Whoever takes on this role must oversee the day-to-day management of on-site operations from start to finish (including pre-planning) and ensure all tasks are carried out with a focus on three key things – meeting timescales, keeping within budget and performing to the expected quality standards.
There’s no doubting that being a Site Manager is challenging but, as with many job roles, when some thought and time is given to being more effective, things can become easier and more enjoyable. If you’re wondering how to do this, read our blog for our top five tips.
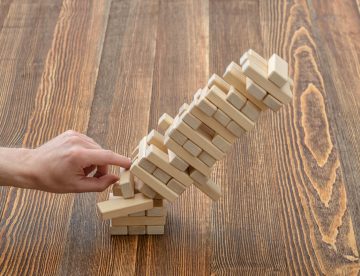
Mistakes can be made at any phase of a construction project. Some may be minor but others can have serious consequences, affecting costs, schedules and, of course, the health and safety of workers. When the stakes are this high, it’s important that any mistakes lead to lessons being learnt, but it’s even more important that they are avoided in the first place. With that in mind, here’s our short guide to avoiding some of the common pitfalls in construction; in other words what NOT to do!