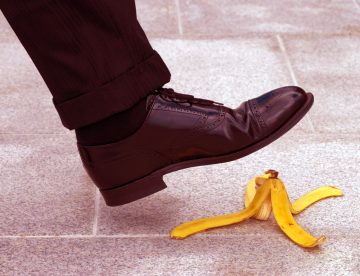
A few weeks ago, we published a blog with some tips about managing and improving something that plays a huge part in every construction project – quality. We looked at how important it is to set out goals, carry out tons of forward planning, create work lists for each and every phase of a project, make inspection plans and to monitor, review and learn from every experience.
However, even with the very best intentions to keep on top of all of this, once a project is underway those intentions can be slipped up and brought to the ground by unexpected obstacles or even by a single mistake that compromises quality and/or safety. As a follow up to our previous blog, today we’re delving into four key factors than can cause such a fall – Systems and audits, Changes, Materials and suppliers, and Human error.
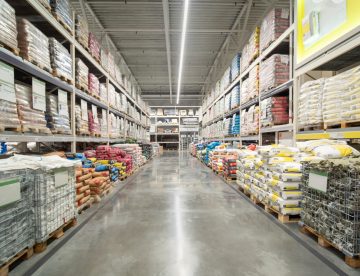
Rigorous safety checks on the materials used to build homes will be enforced by a new national Regulator for Construction Products. Largely brought about in response to testimonies made about some manufacturers of construction materials at the Grenfell Inquiry, the Regulator will have powers to remove materials with significant safety risks from the market; to investigate cases and conduct its own product-testing; and to prosecute companies that fail to follow the rules.